Main navigation
Specially designed for you, this tool will help you estimate, step by step, the thickness of the coating to apply and the quantity fo wire to use in all your projects, whichever corrosion classes you work with and the type of wire selected.
* The figure given above is purely theoretical and is given for information only. It therefore does not engage Zinacor S.A. in any way. In practice, you will have to take into account many technical, design and human factors that will increase the quantity to be used.
Get in touch helps us to understand you better
Rue de Chênée 53 (entrée B)
B-4031 Angleur- Belgique
Telephone +3243666471
Get in touch helps us to understand you better
- Technical advices
-
Electrolytic galvanising / Electroplating
Electrolytic galvanising / Electroplating
Electrolytic galvanising or electroplating is a process for surface treatment using electrolysis. Electrolysis uses an electric current to drive chemical reactions.
The steel part to be treated, degreased and stripped beforehand, is dipped in a bath containing an aqueous solution of zinc salts which will play the role of electrolyte. I.e. it will let through the electric current due to ion motion. The steel part is connected as a cathode to the negative terminal of the generator, and the anode, connected to the positive terminal of the generator, is composed of zinc. Under the action of a continuous current, zinc dissolves and is deposited on the steel part.
The process of electrolytic galvanising or electroplating can be continuous (metal strip, wire, tube) or discontinuous, i.e. in batches (small parts like bolts, nuts, etc.). The discontinuous process takes place in hanging baths or in perforated rotating drums.
The thickness of coating obtained by continuous electroplating is 1-10µm per side, while a coating obtained by discontinuous electroplating varies between 5 and 25µm.
The anti-corrosion protection of a zinc coating can be improved by chromium passivation which gives it a transparent green yellow colour or a straw yellow to metal blue colour (ISO 5002 and NF EN 10152 standards).
The advantages are:
- good adhesion;
- regular coating thickness on the exterior side of parts;
- can be electroplated: stainless steel, cast iron and even plastic.
The disadvantages are:
- reduced cathodic protection due the small coating thickness;
- limited anti-corrosion protection since the lifetime of a zinc coating is directly proportional to the thickness of its layer;
- the inner walls of hollow parts are not or very little protected since the current does not reach inside a steel part and hence there is no zinc deposit in that place (Faraday cage);
- limited to small parts.
Other questions
-
Category :Metallising
-
Category :Zinc rich paint
-
Category :Sacrificial anodes
-
Category :Sherardising
-
Category :Mechanical galvanising
-
Category :Hot-dip galvanising
-
Category :Anti-corrosion performance of different systems
ISO 2063 Standard
Contact
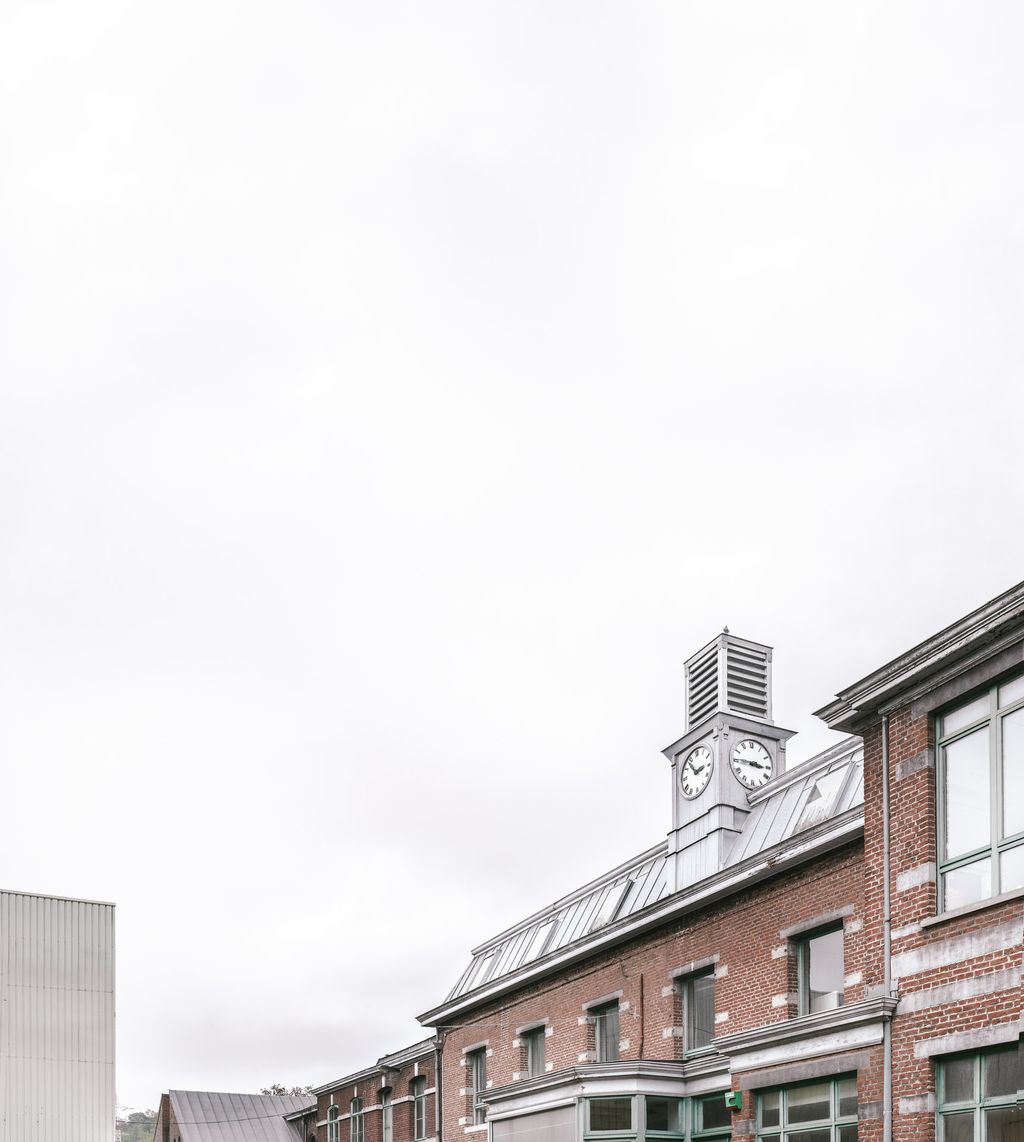
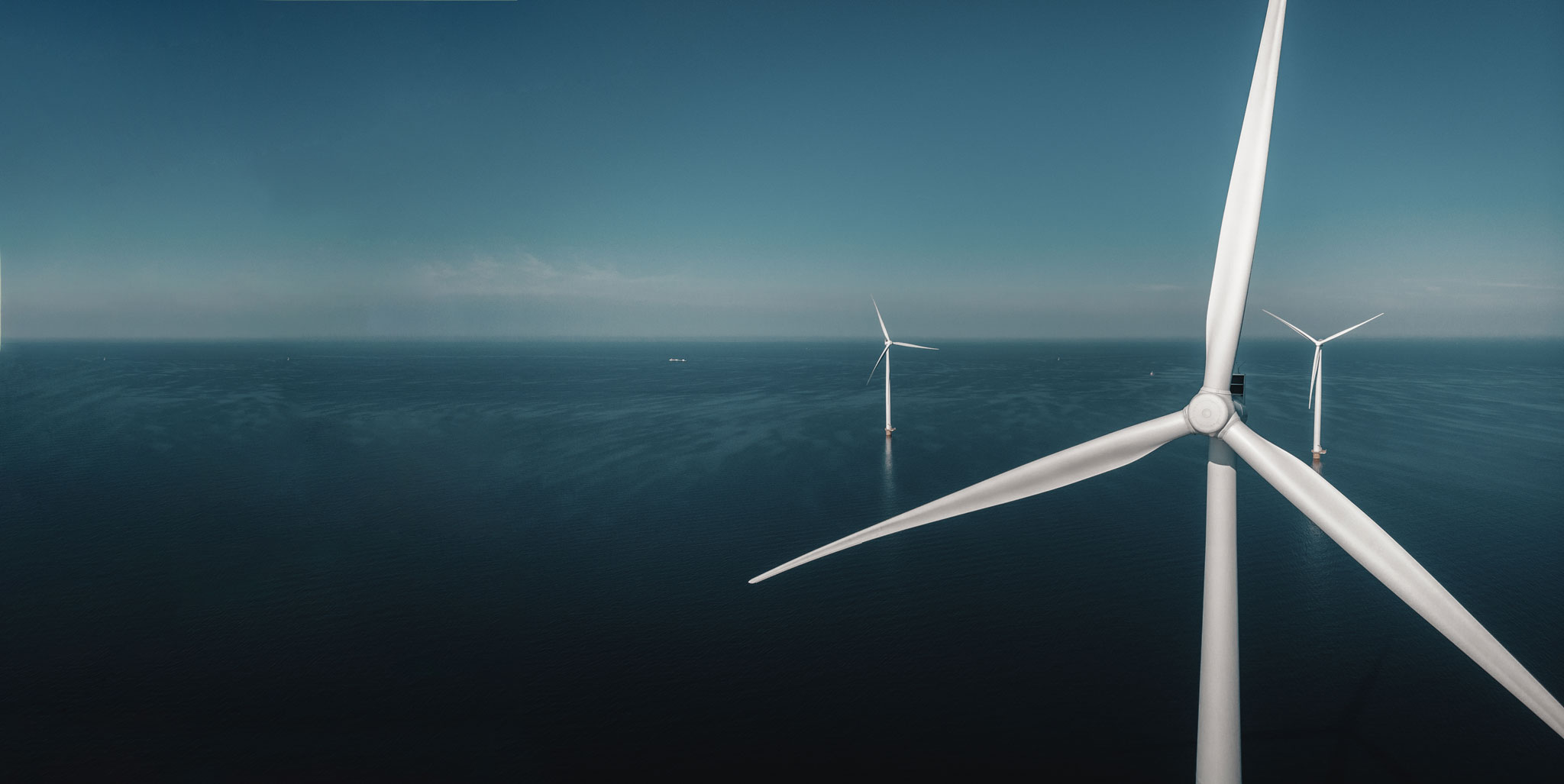
We use cookies to improve your online experience.
For more information, visit our privacy policy